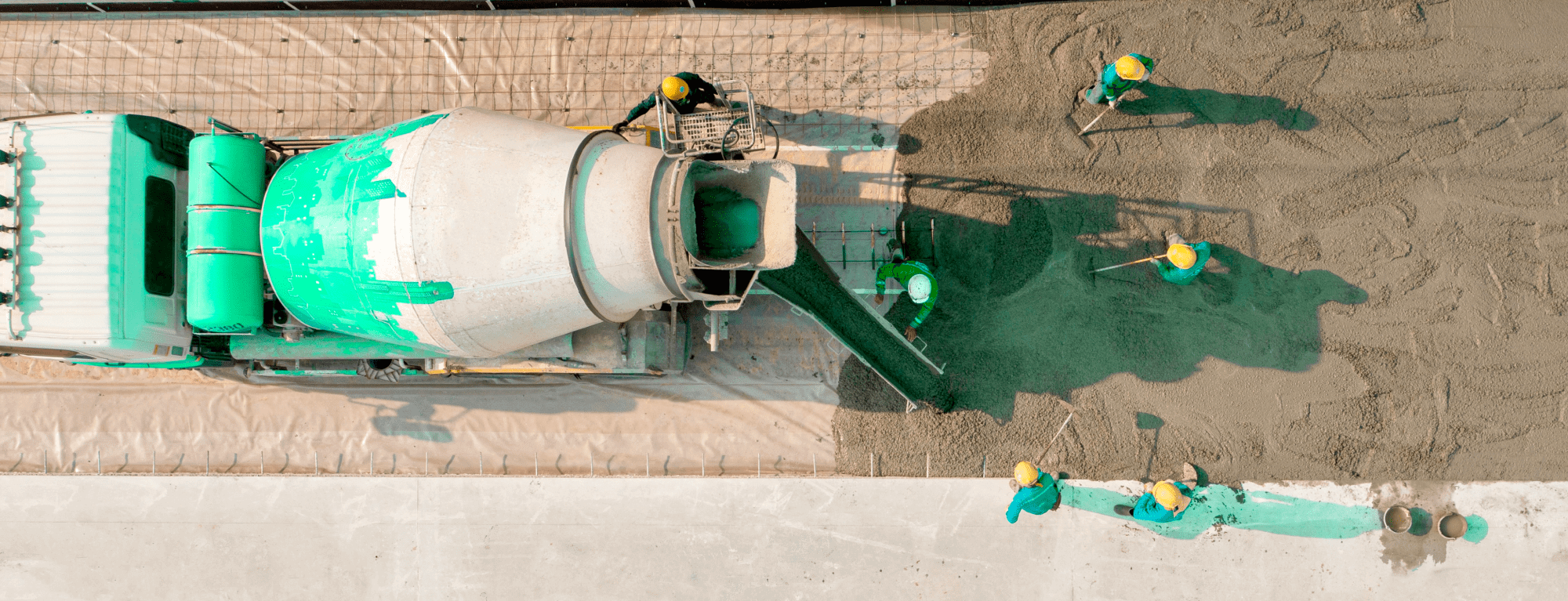
Future development will be built with cement. LC3 provides the opportunity to support self-determination and combat climate change — and philanthropy can help accelerate its deployment.
Cement is the most common building material in the world. Nearly 9,000 pounds of concrete — cement combined with an aggregate such as gravel, crushed stone, or sand — is produced per person per year on average, and its use is increasing rapidly. About half of this concrete is used for roads and infrastructure and the other half for buildings. It is a critical material for meeting growing housing and infrastructure needs in emerging economies worldwide.
Unfortunately, due to the enormous amounts produced, the most common type of cement, known as ordinary Portland cement (OPC), contributes significantly to climate change, comprising approximately 8% of total global carbon emissions. Given the Paris Agreement calls for a 50% reduction of global emissions by 2030, the need to decarbonize the cement industry is urgent.
One central strategy for reducing the emissions intensity of cement involves using supplementary cementitious materials (SCMs) such as fly ash and slag — byproducts from burning coal and refining iron ore — to displace a percentage of the cement. However, these materials are becoming increasingly scarce and expensive, and are already almost fully utilized. There are several next-generation cement technologies under development, but they will not be commercially viable or globally scalable in time to meet the Paris Agreement’s 2030 targets.
There is a solution, however, that can help meet the need for immediate emissions reduction: the use of a low-carbon alternative building material known as Limestone Calcined Clay Cement (LC3). Currently, LC3 is the only cement available for deployment at scale for decarbonizing this industry. Achieving Paris Agreement targets will require producing millions of tons of LC3 before the end of the decade, at a minimum.
LC3: a scalable low-carbon solution for the cement industry
The most carbon-intensive part of cement is the production of clinker, which requires heating limestone to very high temperatures (around 1450° C) to make the material reactive. Producing clinker releases carbon dioxide (CO2) in two ways: first, it burns fuel (usually coal) to reach the desired temperature. Second, even more CO2 (around 60% of emissions) is released when limestone is chemically broken down — more specifically when CaCO3 turns into calcium oxide (CaO) and CO2. A January 2023 explainer from ClimateWorks provides an overview of cement’s climate impact.
LC3 addresses both these sources of CO2 emissions. First, it replaces half of the carbon-intensive clinker with calcined clay and ground limestone, neither of which have process emissions. Second, the clay is calcined at a much lower 800° C, which reduces emissions and uses less expensive energy. LC3 can reduce CO2 emissions by up to 40% compared with OPC. Additionally, calcined clay reacts with lower-grade limestone, which simplifies access to raw materials for making LC3. Figure 1 below illustrates the significant CO2 savings obtained by replacing clinker with calcined clay and limestone.
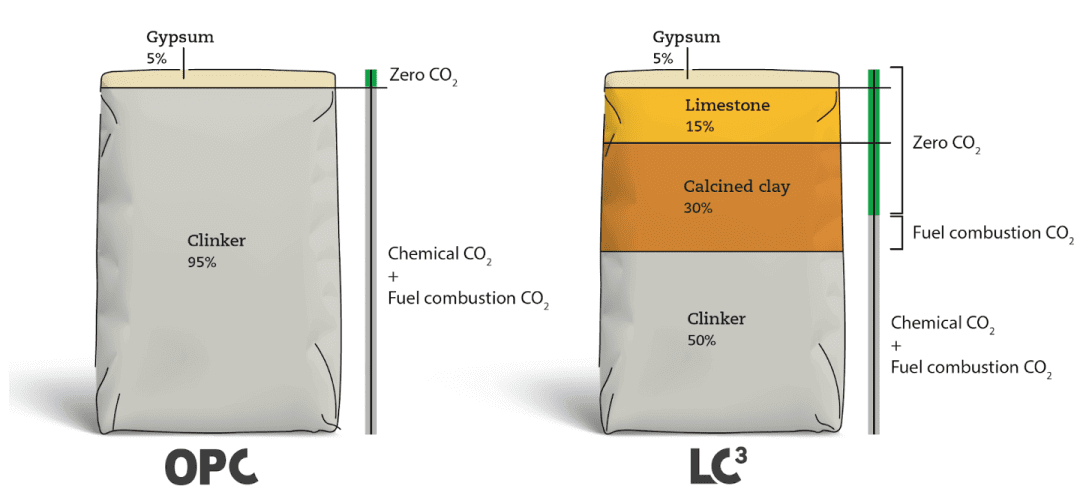
As a concrete example, if the 768-meter-long Madre Laura Bridge in Colombia were built with LC3 rather than OPC, it would have saved 9,240 tons of CO2 — equivalent to 15,500 passengers flying from San Francisco to New York City. If the cement industry widely adopts the use of LC3, this technology can help prevent up to 500 million tons of CO2 emissions per year by 2030. That figure is expected to increase as research advances and as LC3 potentially replaces even larger amounts of clinker.
A potential game-changer for durable infrastructure
Overall, LC3 performs equivalently, lasts longer, and is a more cost-effective and dramatically more climate-friendly option than conventional cement. Compared with OPC, LC3 provides excellent early strength, similar to typical concrete mix designs, which means it will not slow down construction schedules. After just 7 days, LC3 performs better than conventional cement, and it maintains parity through 90 days, as shown in Figure 2.
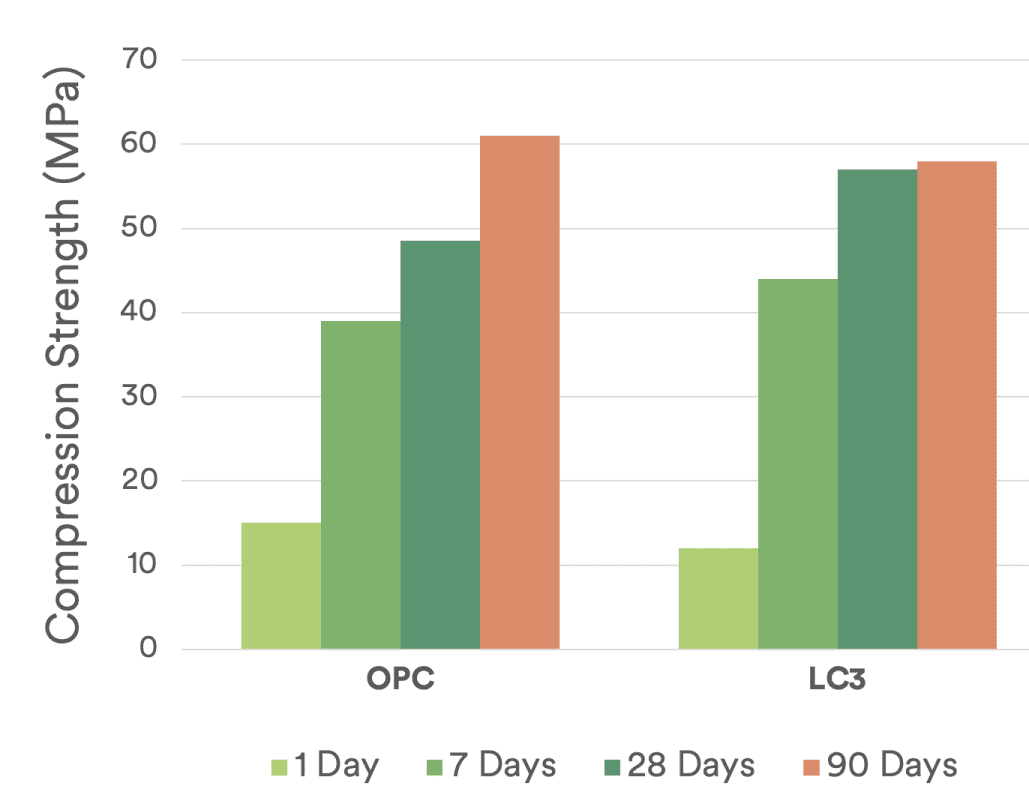
LC3 has a high chloride penetration resistance and presents a dense microstructure with high surface resistivity, which makes it ideal for harsh marine and desert environments. It is also less pervious, which means that water and salts do not get into the concrete to cause cracks and deterioration. Blocks of concrete made with LC3 have been tested in the ocean on the shores of Cuba for nearly 10 years now and show no sign of corrosion.
These characteristics make LC3 a potential game-changer for more durable infrastructure. For example, in Louisiana, where there are many roads and bridges in saltwater marine environments, LC3 performs well on resistance tests to demonstrate imperviousness as required by the Department of Transport (DOT). Tom Van Dam, a civil engineer working with state DOTs, explains that “LC3 creates more durable concrete, meaning freeways and other infrastructure will last longer, and it installs just like regular concrete, using the same equipment and techniques. It’s an urgent solution to reduce emissions quickly.”
The next boom in construction: The Global South
Today, more than 1 billion people are inadequately housed and the need for construction will only increase due to urbanization and population growth in the coming decades. The majority of new construction will occur in the Global South, as illustrated in Figure 3. This trend will accelerate due to the enormous needs of emerging economies in Asia and especially in Africa, where the population is expected to increase by 1 billion by 2050.
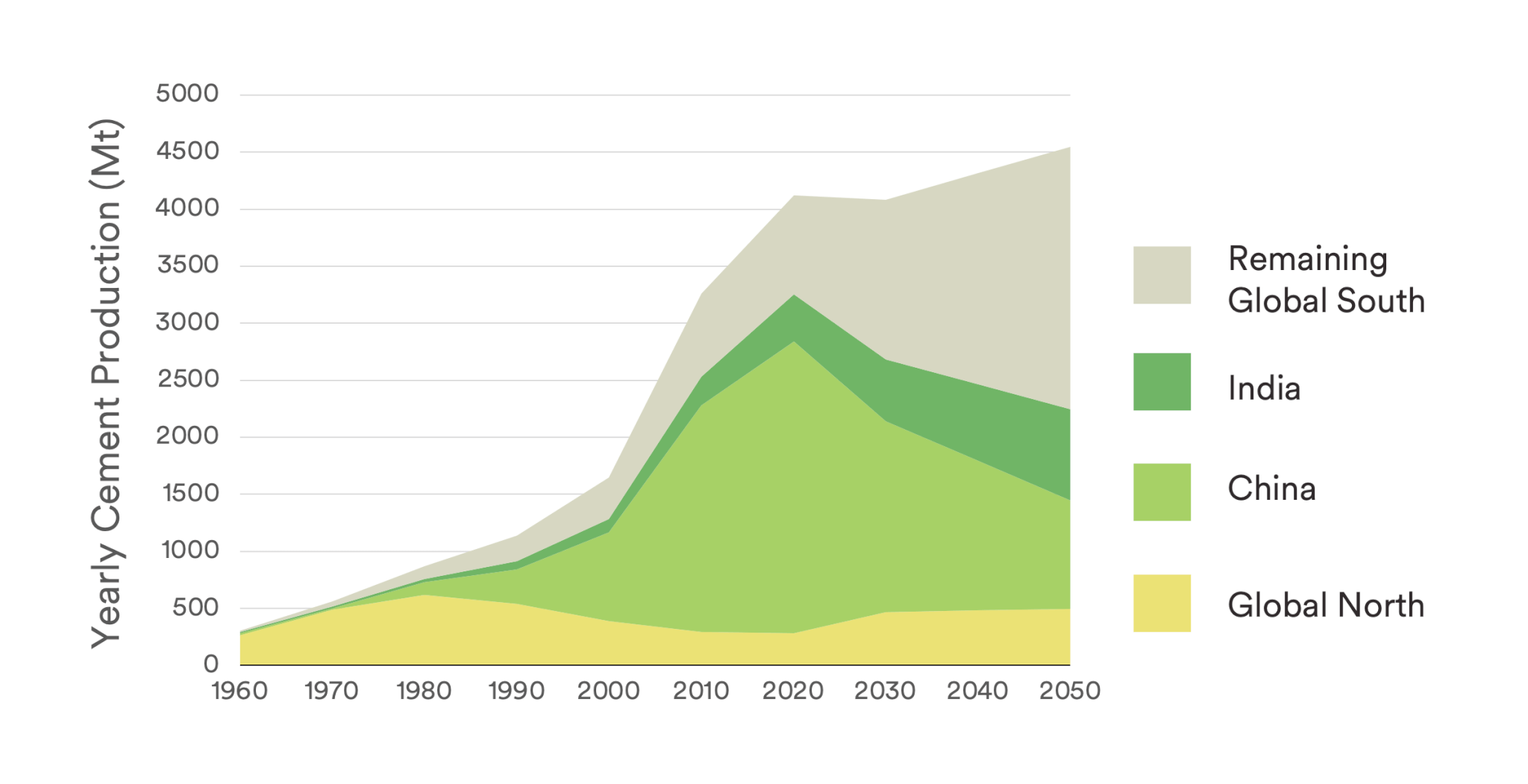
Fortunately, clays are the weathering products of all rock types. As a result, they are widely available close to the Earth’s surface in all geological settings. Clays that contain kaolinite, which are the most suitable clay types for LC3, are abundantly available in countries in the Global South (see yellow areas in Figure 4). These regions are where most of the increase in demand for cement is forecasted to occur, and the use of locally available material will provide major economic and climate benefits.
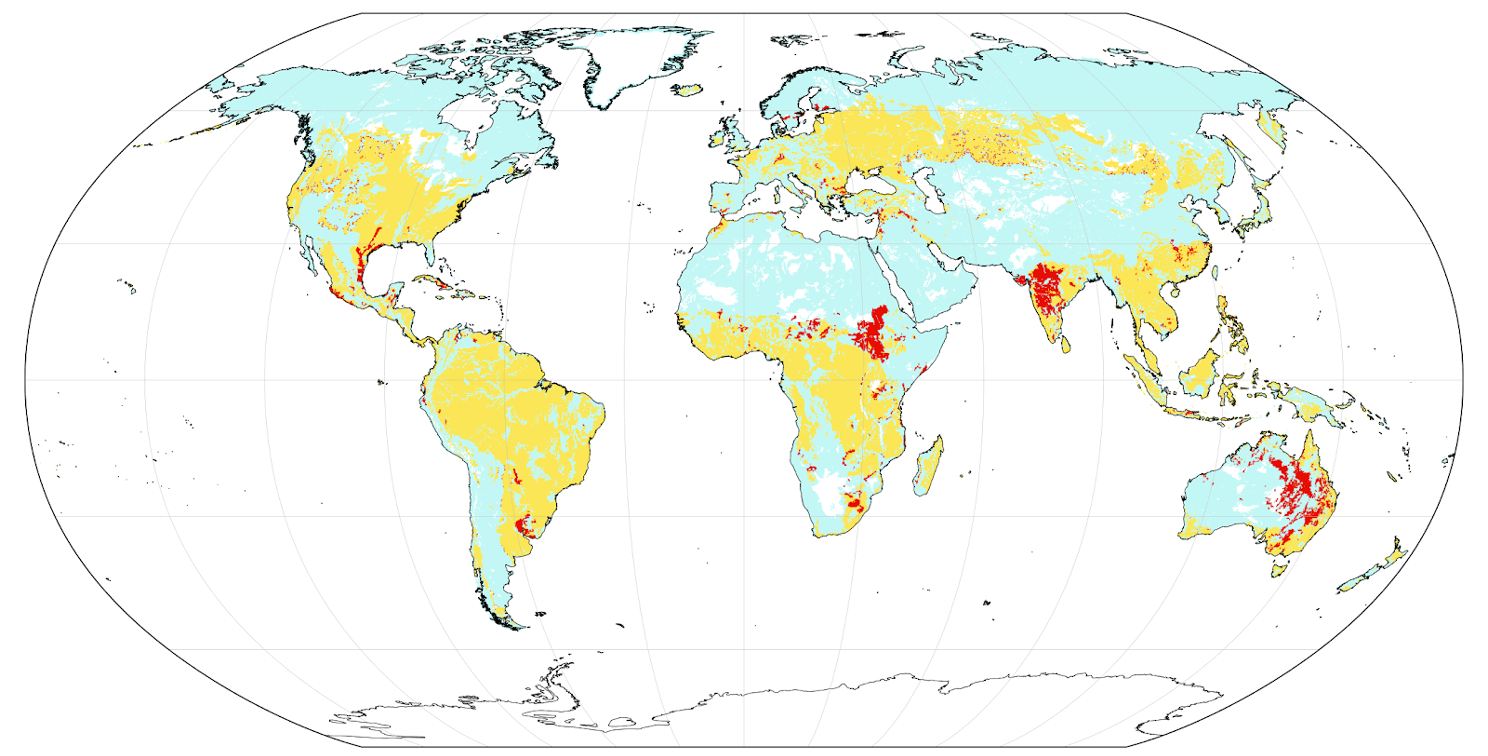
A critical moment for scaling up LC3 deployment
LC3 is a well-known and proven solution. The critical task now is to demonstrate to cement producers that there is demand for the product — and to encourage designers, owners, and contractors to ask for this low-carbon alternative. Conveniently for cement producers, switching to producing LC3 only requires minimal changes to infrastructure in existing plants, making the operational transition straightforward and low-cost. At least seven companies currently produce LC3, including Argos in Colombia, Holcim in France, and Ash Grove in the United States, with more than 20 additional companies expected to follow.
“We are now producing LC3 in our standard rotary cement kiln and we’re planning to expand rapidly,” says Cheng Qi, Ash Grove Technical Center Director. “More than 100 power plants have stopped burning coal, making the availability and quality of SCMs like fly ash decrease. Calcined clay cement is the gold standard for durability used on freeways in the Northeast.”
A critical challenge is getting the many relevant parties — cement producers, building owners, architects, engineers, code authorities, and contractors — to take a broader perspective focused on transforming the entire building industry. The design and construction community has historically focused on the one project they are working on at a given time. To meet global climate goals, there needs to be a shift in mindset towards transforming the industry as a whole, not just producing exceptional one-off structures. This requires a focus on transformative materials that are affordable and can scale globally rather than hypothetical replacements for cement that are not yet affordable or ready to commercialize around the globe.
One key approach for transitioning to low-carbon building materials is to generate enough demand and incentives to change the status quo. In recent years, several policy advancements have helped create these incentives, especially in the United States. At the federal level, public funding from the Inflation Reduction Act provides a critical leverage point to transform the industry toward materials with significantly lower embodied carbon. Likewise, Buy Clean policies require the procurement of low-carbon materials on public construction projects. At the state level, policies such as the New Jersey Low Embodied Carbon Concrete Leadership Act (LECCLA) encourage innovative new low-carbon mix designs with financial incentives, while California’s SB596 calls for detailed road maps to get to net-zero cement by 2045.
Philanthropy can play a critical role in providing initial investment and education to help move the sector toward a low-carbon future. Additionally, philanthropy can serve as a convener by bringing together various actors in the building industry that typically do not interact with one another. These efforts create opportunities to share the latest research and developments in the field and provide venues for honest exchanges on how to collaborate, answer questions, and overcome challenges. Philanthropy can also facilitate testing and demonstration projects to provide hands-on experience with LC3, increasing confidence across the entire value chain.
Responding to climate change involves swift action on a global scale. Achieving the emissions reduction targets outlined in the Paris Agreement will require all sectors — including the buildings sector — to make revolutionary changes. LC3 is a well-proven solution for decarbonizing the cement industry that uses existing production infrastructure and is globally available. Now is the time for an all-out deployment.